This post was updated in January 2025.
Organising a factory relocation project is a significant task for any business. With multiple factors to consider, departments to align, and challenges to overcome, relocating a factory is one of the most challenging projects a company may face.
With the right planning, management and execution, there’s no reason why factory relocations can’t be a success. Working with a specialist partner can ease the strain on your business and ensure things run smoothly.
At Flegg Projects we do just that.
In this guide we’ll discuss some of the main considerations when planning factory relocations, along with advice on how to select a suitable partner to work with.
8 key steps for planning factory moves
1. Plan early
You can never start planning too early for the relocation of a factory. With many components to consider, aim to give yourself the maximum time possible to coordinate the move. Take a meticulous approach to planning and allow enough time to review and make changes to the plan.
2. Communication
Where possible, engage with your workforce, stakeholders and customers. Effective communication early on can help to ease difficulties further down the line. Explain the reasons for the move, how it may affect them and what to expect. Provide regular updates and be open to discuss new ideas.
3. Establish a team
Bring in a skilled project team who are capable of coordinating and executing the intricacies of a move. Choose people with dedicated specialisms, who can advise, plan and coordinate in their specific area, with a project manager assigned to take overall responsibility for the relocation project.
4. Bring in external partners
It’s important to recognise where additional skill and expertise is needed. Get clear early on about what support you need and find suitable companies to partner with. The earlier you do this the better, allowing you to benefit from the full breadth of their experience and knowledge.
5. Develop a project plan
Create a project plan that contains as much detail as possible. Include critical paths with clear expectations and timelines. Keep your plan updated and circulate to everyone involved in the project to ensure the different stages and departments align. A project manager will typically ensure everything stays on track.
6. Safety and risk assessment
Mistakes can be costly, particularly when heavy machinery is involved. Conduct thorough site surveys and risk assessments to ensure your factory relocation is safe and the risk of damage and injury is mitigated. Seek specialist advice where needed.
7. Review your operations
A factory relocation is a great time to re-evaluate your logistics and current processes. Consider ways to improve the efficiency, output and quality of your service, and build these into your layout plans. Engage your workforce – as the people working on the ground, they may be able to provide some interesting insights
8. Transportation of heavy assets
Work with a specialist machinery mover, who can manage the disassembly, transportation and installation of your most valuable assets. They will ensure your machinery is transported safely and with minimal damage risk, adhering to any importation laws (for overseas moves) and providing packing and storage facilities where needed.
Finding the right support
Choosing to work with a factory relocation company can make all the difference in how safe, smooth and efficient a relocation project runs. Look for companies with a proven track record in managing complex factory relocations and utilise their expertise.
When choosing a partner, we recommend looking for the following qualities:
Project management services
Proven expertise managing factory relocations, with the know-how to plan a move meticulously and with minimal disruption.
Expert machinery movers
Providing skilled engineers and high-quality lifting equipment to safely and efficiently move heavy machinery between multiple locations.
Suitable storage facilities
Warehousing facilities suited to heavy machinery storage should the need arise.
Packing services
A skilled, quality and thorough approach to packing that adheres to customs requirements.
Documentation support
Knowledge of regulations and the required documentation to support both national and international factory relocations.
Safety and risk assessment
A meticulous approach to safety, conducting site surveys and risk assessments where appropriate, with proven strategies to mitigate injury and damage.
Effective communication
The ability to effectively communicate in multi-departmental operations.
Factory relocation services at Flegg Projects
Flegg Projects has 50 years’ experience in planning and coordinating plant and factory relocations on both a national and international level. We are an independent business with knowledge and expertise in all areas of machinery moving. Our aim is to provide a quality service that eases the pressure placed on you.
One of the main benefits of working with Flegg Projects is our fully flexible approach – we understand that every business functions differently, and our service will be tailored to your requirements. Our team will work in partnership with you to ensure your relocation project is both efficient and smooth.
Our service includes:
- Skilled management of your factory relocation to ensure production can continue and there are minimal interruptions
- Use of high-quality equipment and skilled engineers to manage the transportation of heavy machinery, including packing, disassembly and installation
- Support with both small or large-scale projects, from moving a single machine to full site clearance and relocation
- The capability and knowledge to support both UK-based and international factory relocations
- Principal contractor services and turnkey solutions, along with a range of additional services
A case study
The challenge
A UK publishing house approached us to move their book binding machinery from the UK to Australia. To adhere with Australia’s importation rules, machinery had to be cleaned and certain packaging had to be heat-treated. Importation documentation had to be completed effectively to ensure no complications arose during transit.
The solution
We are very familiar with the importation regulations in Australia, and our team was able to support the client throughout. All documentation was completed, and we transported the machinery to our Aylesbury facility for cleaning and packing treatment. We loaded the machinery onto containers and worked with a freight forwarder to ensure both the machinery and documentation made a successful journey
The result
Our team worked efficiently, and the machinery was transported to our Aylesbury warehouse, cleaned, repacked and loaded onto 6 containers in just 7 days! The machines arrived safely in Australia, resulting in the client requesting additional support from us at the original site.
Read more about this case study.
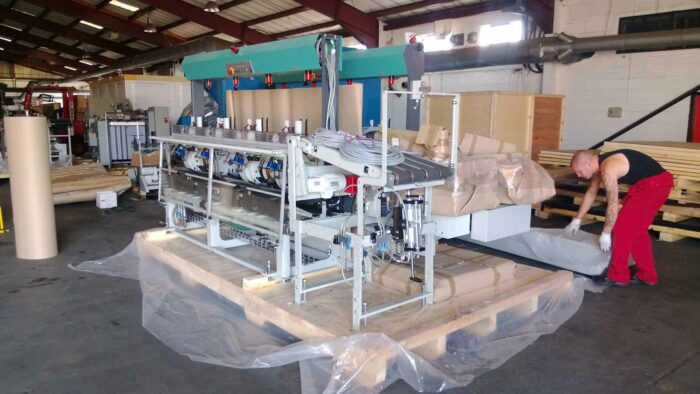
Contact us today
If you are planning a factory relocation or would like to find out more about the service we provide at Flegg Projects, get in contact with us today.
Our experienced and knowledgeable team will be happy to guide you.
Reach out to our team to discover how we can support you – you can call us on 01296 630234, email us at info@fleggprojects.co.uk or complete our Project Enquiry form.